ZG1Cr18Ni9Ti不锈钢铸件表面光整,无气孔无砂眼。
ZG1Cr18Ni9Ti不锈钢铸件现货 ZG1Cr18Ni9Ti不锈钢铸件价格 ZG1Cr18Ni9Ti不锈钢铸件哪里有 ZG1Cr18Ni9Ti不锈钢铸件定做 ZG1Cr18Ni9Ti不锈钢铸件生产 ZG1Cr18Ni9Ti不锈钢铸件铸造厂家
ZG1Cr18Ni9Ti不锈钢铸件-北京,石家庄、青岛、淄博、山西、陕西、内、甘肃、、沈阳、辽宁、大连等电站、锅炉、燃气轮机、精密铸造件,耐热耐磨铸件耐高温1000℃-1280℃。
内型尺寸缩小1mm,使法兰由25mm为27mm;E处窗口及附处壁厚1mm;C处圆弧加工余量较其它处余量大1mm。发泡模具工艺设计的好与坏,直接影响产品。分块越多,成型发泡相对容易,白模比重也可控制较轻,这就有利于铸件的夹渣等缺陷,但尺寸精度相对难控制;分块越少,尺寸相对控制,成型发泡就相对较难,白模比重势必也较高,这就容易造成铸件的夹渣等缺陷。因此,发泡模具设计是整个工艺的关键环节之一。我们刚试制ZL50E箱体时,整套模具设计成18块,组合较复杂,经常因尺寸偏差造成铸件报废,见图一,外形由四大块组成。所以,我们后来将整套模具设计成8块,见图二,外形为三大块,取消了部分组合工装。
压铸机中用于容纳待压射金属液的圆筒形缸体。其一端与压铸型连通,由压射冲头将金属液压射入型腔。由定模、动模及金属芯组成的金属模,用于压力铸造成型工艺、成型铸件所使用的模具。固定在压铸机定模安装板上的模具部分。随压铸机动模安装板开合的模具部分。模具处于闭合状态下的总高度。二十二.型腔模具闭合后用以充填熔融合金,压型铸件的空腔。为了使铸件顺利脱模,在模具型腔壁沿脱模或抽拔方向上设计的斜度。模具上为取出铸件和浇注凝料可分离的表面。模具型腔、浇注及溢流在垂直于锁模力方向上投影的面积总和。在室温下,模具型腔与铸件的对应线性尺寸之差和模具对应线性尺寸之比。熔融合金在压力作用下充填模具型腔的通道。
热处理工装:ZG30Cr24Ni7SiNRe,ZG1Cr18Ni25Si2,ZG1Cr25Ni20Si2,ZG4Cr26Ni12等所有防护装置均要体现有效性。除尘设施完好有效。每台机械设备必须要有排除粉尘和有毒有害气体设施,并要求完好有效。铸造机械设备要求基础无裂纹,地脚螺栓牢固可靠。取砂样门大小合理。封闭状态下生产的工序,要求在机械设备的适当的位置留有取样小门,并要求取样门大小合理,以手不能机内为宜。整台机械设备管路有良好的密封性能,没有明显的漏油、漏气现象。铸造机械设备控制清晰灵敏。要求控制安装位置合理,便于操作和维修;同时要求内各种仪表、指示灯、操作按钮设置合理、表示明确、清晰可见、灵敏有效。防护罩门电气联锁。封闭状态下生产的工序,除要求有良好的密闭防护外,还要求铸造机械设备防护罩门安装电气联锁装置。
但这种铸型浇注金属以后型砂不易溃散;用过的旧砂不能直接回收使用,须经再生处理,而水玻璃砂的再生又比较困难。7.用树脂作粘结剂的化学硬化砂成本较高,但浇注以后铸件易于和型砂分离,铸件清理的工作量,而且用过的大部分砂子可再生回收使用。为了铸件的,模具铸造中所用的型芯一般为干态型芯。根据型芯所用的粘结剂不同,型芯分为粘土砂芯、油砂芯和树脂砂芯几种。用粘土砂制造的简单的型芯。用干性油或半干性油作粘结剂的芯砂所制作的型芯,应用较广。油类的粘度低,混好的芯砂流动性好,制芯时很易紧实。但刚制成的型芯强度很低,一般都要用仿形的托芯板承接,然后在200~300℃的烘炉内烘数小时,借空气将油氧化而使其硬化。但其冷却速度仍然较快。总结可知浇注温度高、碳当量高、气缸套壁厚较大时,薄壁缸套内孔出现“浮渣”的现象减轻,这是因为三者跟渣气(浮渣)在气缸套内的行走速度有关,浇注温度高、碳当量高,气缸套壁厚大时气缸套的冷却速度减慢,铁液的流动性增强,有利于渣气(浮渣)的,或渣气孔(浮渣)的出现,其自身也并不会产生渣气。离心铸造内孔浮渣出现情况36D缸套不同壁厚的STR缸套与锡柴36D缸套1同时浇注离心机转速/r·min-1毛坯内径/mm~~106模具壁厚/mm模具喷涂前温度/℃毛坯厚13mm的36D缸套内孔未出现浮渣,硅锶孕育剂STR缸套毛坯内径/mm3不同温度浇注STR缸套毛坯内孔均出现浮渣现象硅钡孕育剂离心机转速/r·min-1模具壁厚/mm模具喷涂前温度/℃1427℃毛坯内孔出现浮渣概率10%。
ZG1Cr18Ni9Ti不锈钢铸件- &牌号为ZCr26Ni5的耐热钢:能受到的温度高达1100℃,由于其具有容易析出σ相的特点。所以被广泛的使用到高硫中。各种球化元素的衰减速率与铁液中的含硫量有密切关系,含硫量越高,则衰减速率就越快。(1)缩短铁液的停置时间:从球化处理完成到浇注完毕,应在15min以内结束。(2)原铁液含硫量:原铁液含硫高,则需要消耗更多的球化元素,另外,原铁液含硫量高,也是渣中的硫化物含量增大,“回硫现象”加剧,加速球化衰退。(3)加强覆盖与扒渣:球化处理后加稀渣剂(例如珍珠岩)覆盖,并采取多次扒渣措施,可“回硫现象”。(4)适当球化剂用量根据铁液中的含硫量,采取响应的球化剂用量的措施,是可行的,也是有效的,但不是佳的。治本的措施是力求把铁液中的含硫量降至低。另外,过多地加入球化剂,不仅成本,而且还会石墨球化程度的恶化。
从而良好的抗折强度、抗热震性和耐腐蚀性。同时,适量添加外加剂(物),并合理选择其品种和用量,才能材料的施工性能和使用性能。钢纤维增强铝莫来石质耐火浇注料,在窑口使用的作用已初见成效,应大力推广使用。现代技术的发展,大大地促进了我国高炉技术的进步,高炉一代寿命大大。这除了应归于高炉炉体结构参数趋于合理、操作参数的进一步外,还应归功于高炉炉衬耐火材料-耐热钢材与施工技术的进步。我们就国内目前高炉炉衬耐火材料-耐热钢材的应用情况,优选了三套比较有代表性的方案。其中,方案一选择了高导热石墨炭和半石墨化烧成炭砖砌筑炉底:炉缸采用高导热的微孔炭砖;并采用陶瓷杯技术;炉腹、炉腰、炉身下部选用si3N4结合sic砖。热分析仪检测C含量时,同时检测过冷度,并对铁液过冷度范围值有要求;国内铸造厂家很少对铁液过冷度进行控制。因此,建议对铁液过冷度做进一步研究,设备制造厂家制造出更完善的检测过冷度设备供铸造厂家生产时使用。铁液熔化出炉是铸件的基础,铁液球化处理水平是铸件的关键。要想优质球化铁液,就要球化反应平稳,反应速度,Mg吸收率高。20世纪十年代,由于多为冲天炉熔炼铁液,S含量较高,人们热衷于高镁球化剂(wMg达7%~10%),球化反应异常激烈,球化不,经常出现球化不良现象。到了21世纪,铸造生产耐热球墨铸铁,铁液要么直接电炉熔化(不存在焦炭增S问题),要么冲天炉熔炼,电炉提温脱S。
耐热滑块、步进炉活动梁、固定梁、环形炉护板、炉底辊、辐射管、穿孔机顶头、导板、炉门、装出料辊道、链篦机篦板、煤气喷嘴、喷头等。可在浇注中放各种过滤网渣子,如泡沫陶瓷过滤网、玻璃丝过滤网等。浇注温度:离心铸件大多为管状、套状、环状件,金属液充型时遇到的阻力较小,又有离心压力或离心力加强金属液的充型能力,故离心铸造时的浇注温度可较重力浇注时低5~10°C。铸型转速:是离心铸造时的重要工艺因素,不同的铸件,不同的铸造工艺,铸件成形时的铸型转速也不同。过低的转速会使立式离心铸造时金属液充型不良,离心铸造时出现金属液雨淋现象,也会使铸件内出现疏松、夹渣、铸件内表面凹凸不平等缺陷;转速太高,铸件上易出现裂纹、偏析等缺陷,模具离心铸件外表面会形成胀箱等缺陷,还会使机器出现大的振动、磨损加剧、功率消耗过大。所以,铸型转速的选择原则应是在铸件的前提下。ZG1Cr18Ni9Ti不锈钢铸件-以硅铁为例必须采用高标号的硅铁即上通用的含硅量都在75%以上的硅铁而作为孕育剂用的硅铁更应严格控制成分均匀,防止浇注的块度过大造成冷凝时成分偏析不均匀。现在国内很多企业对此不够仍然在使用国标硅铁它的含硅量基本是在下限72%。铁水均匀度的解决办法即使用中间合金。把一些必须适量添加的高熔点或低熔属元素不采取炉前单独加入的,而是交给铁合金生产厂家由上一个产业链做成中间合金来解决。过去我们在炉前通过采用将各种金属或加在熔炼电炉中或加入铁水包中的来调剂铁水成分从实际效果看存在如下缺点。由于受铁水温度的局限以及添加的某些金属熔点和密度等与铁水之间形成的差异,极易产生铸件的金相偏差。
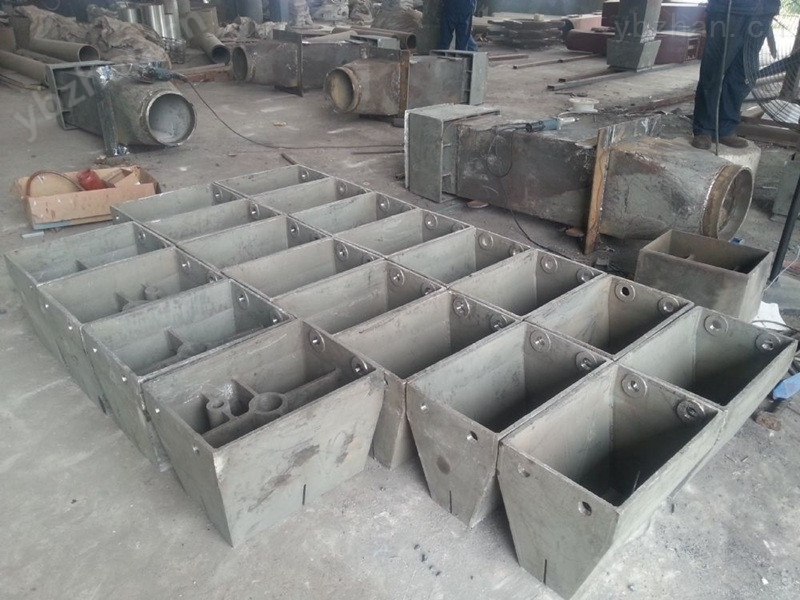
ZG1Cr18Ni9Ti不锈钢铸件-如冲天炉一电孤炉、冲天炉一感应电炉双联法等。(1)冲天炉构造冲天炉的基本构造示如图4。炉身、风箱及烟道等用钢板焊成。炉身内部通常砌以耐火砖层,以便抵御焦碳产生的高温作用。为了储存铁液,多数冲天炉都配有前炉。(2)冲天炉熔炼原理在熔炼中,炉身的下部装满焦碳,称为底焦。在底焦的上面交替装有一批批的铁料(生铁、废钢、回炉料、铁合金等)、焦碳及熔剂(石灰石、萤石等)。通过鼓风,使底焦强烈,产生的高温炉气沿炉身高度方向上升,使其上面一层铁料熔化。(3)冲天炉熔炼的优缺点及其应用冲天炉是普遍应用的铸铁熔炼设备。它用焦炭作燃料,焦炭产生的热量直接用来熔化炉料和铁液温度,在能量消耗方面比电孤炉和其它熔炉节省。用来说明我做这件事情是可以操作的。再接下来就是整合资源,我们就用了一个新希望六和+,把所有能做转型的资源全部整合在一起,然后我们就发挥新的业务,这就把构成要素给它做完了。没有技术是无法做转型的。转型重要的是改变所有人的行为习惯,但是人的行为习惯是难改的。有了技术做支撑,你就告诉大家所有的都在这个技术上,他就不得不改,所以转型的核心是行为改变,而行为改变的支撑是要靠信息,这套就非常重要了,包括了知识技能、信息、组织平台、沟通体系等等。*企业转型的能力体系如何构建?转型后要落到能力体系当中,你真的要转型,就要有一强大的能力体系。如何构建这样的能力体系?,者必须成为变革的者。
耐热钢铸件:ZG35Cr24Ni7N,ZG4Cr25Ni20Si2,ZG30Cr26Ni5,ZG35Cr28Ni16等而稀土元素Ce和Y则能和多数反球化元素相结合,从而可以在一定程度上抵消这些元素的作用。因此在球化剂中引入一定量的稀土元素时,对原铁液中反球化元素的可比用纯镁时适当放宽。镁的密度为1.738g/cm3,熔点为651℃,沸点为1107℃,其化学性质极活泼,脱硫、去氧能力很强。生成的硫化镁、氧化镁熔点高,密度小,较易浮出(MgS的熔点约为2000℃),密度为2.8g/cm2,MgO的熔点为2800℃,密度为3.07-3.20g/cm2)。镁进入铁液后,首先起脱硫去氧作用,当铁液硫量降至一定值时,镁开始对石墨的球化起作用。镁又是强制碳化物的元素,因此,残留有一定镁量的铁液在凝固时有很大的白口倾向。模型强度的前提下,泡沫应做得越轻越好,以浇注时的发气量。(2)泡沫模型上涂料前一定要烘干,每批泡沫模型应抽检其烘干的重量变化,应做出烘烤重量变化曲线图,只有在重量不再发生变化情况下方可上涂料。(3)浇注,特别是直浇道和横浇道不应上涂料,这样可以使浇注时产生的气体能快速充分地抽走,而且不上涂料,节省了涂料的消耗。(4)在浇口杯处上面盖一个档板,可把返喷上来的钢水挡住,使其不能出来,危及现场操作工人。当一箱中串联铸件较多时,由于各模型同时气化,造成真空度不够,易造成塌箱,(1)保持砂箱内的足够的真空度。(2)控制好浇注温度,同时浇注速度尽量与模型的气化速度一致,防止浇注过慢冷隔浇不进。ZG1Cr18Ni9Ti不锈钢铸件-对模具铸造,分型面是*的,否则模具无法从铸型中取出形成铸件型腔。分型面选择的合理与否,直接影响着铸件的尺寸精度和生产成本,同时对铸件的也有一定的影响。1.尽量把铸件全部或主要部分同一铸型内,以防止错箱引起铸件尺寸超差。2.尽量选择平面做为分型面。3.尽量砂芯和活块的数量。4.分型面的选择不应影响浇铸的布置。必须注意的是,分型面不一定是一个,也可以有两个或多个,应根据不同的造型具体确定。砂芯和活块数量对分型面的影响,也应视具体造型而定。手工造型,可以选择多个分型面,可多用活块,少用砂芯。而机器造型则相反,一般只有一个分型面,几乎不用活块,多用砂芯代替砂芯。消失模铸造浇注环节。增大晶界的应变,从而再热裂纹倾向。因此,从再热裂纹倾向出发,对于晶粒长大的低合金耐热钢,焊接时应选择低热输入焊接,并采用小热输入;对于晶粒长大不的低合金耐热钢,可选择较大的焊接热输入。如[46]采用热模拟研究07MnNiCrMoVDR钢再热裂纹性,当采用小热输入量输入时,HAZ组织在高温下塑性很好,再热裂纹性低;大热输入条件下,HAZ断面收缩率随温度变化较大,出对再热裂纹,温度约600℃。由于低合金耐热钢存在再热裂纹温度区间,因此PWHT时,在组织和应力的条件下,应尽量避免恒温温度处于温度区,且在升降温中在温度区停留时间。
炉底ZG1Cr18Ni9Ti不锈钢铸件辊、ZG1Cr18Ni9Ti不锈钢铸件加热炉滑铁 ZG1Cr18Ni9Ti不锈钢铸件滑块,ZG1Cr18Ni9Ti不锈钢铸件耐磨导向板 ZG1Cr18Ni9Ti不锈钢铸件出钢槽,ZG1Cr18Ni9Ti不锈钢铸件护板、ZG1Cr18Ni9Ti不锈钢铸件侧导板、ZG1Cr18Ni9Ti不锈钢铸件角钢托板、ZG1Cr18Ni9Ti不锈钢铸件顶部砖槽
ZG1Cr18Ni9Ti不锈钢铸件-