一、全流程无菌化设计,构建生物安全洁净屏障
作为符合 ISO 14644-1 Class 7 洁净等级与中国 GMP 无菌制剂生产要求的核心装备,生物工程反应釜高低温一体机从材料选型到系统架构贯彻生物安全理念。主体管路采用 316L 不锈钢 BA 级卫生管(内壁粗糙度 Ra≤0.2μm),连接方式采用全自动轨道焊接(焊缝经内窥镜检测无缺陷),并配备 CIP/SIP 在线清洗灭菌系统:支持 75℃纯化水循环清洗(流量 10L/min,接触时间 30min)及 135℃饱和蒸汽灭菌(F0 值≥12),配合管路内壁 0.5mm 厚度电解抛光层,消除微生物滋生死角。
关键部件采用德国进口无菌级组件:食品级硅橡胶密封件(通过 USP Class VI 生物相容性认证)、0.22μm 聚偏二氟乙烯(PVDF)除菌过滤器(截留效率≥99.999%),搭配紫外线杀菌模块(波长 254nm,照射强度≥40μW/cm²),对循质进行实时动态灭菌,确保系统生物负载<10CFU/100mL(依据《中国药典》2025 版通则 1121 检测)。
二、精准智能温控系统,动态模拟发酵代谢曲线
搭载生物工艺专用 PID 控制模块,融合发酵过程动力学模型,实现 -10℃~150℃宽温域精准控制(控温精度 ±0.1℃)。支持两种专业控温模式:
1. 分段程序控温模式
可预设 50 段独立温度曲线(每段时长 1min~24h 可调),内置酵母发酵、大肠杆菌表达、CHO 细胞培养等 10 种典型工艺模板。以单克隆抗体制备为例,可自动执行:
2. 动态补偿控温模式
通过实时采集 pH 值(精度 ±0.01)、溶氧(DO,精度 ±1%)、生物量(OD600,分辨率 0.01)三参数,系统自动调整加热 / 制冷功率(调节精度 1%)。在疫苗生产的病毒培养环节,当病毒滴度进入对数增长期(每小时提升 1.5log),温控系统可动态补偿代谢产热,将温度波动控制在 ±0.05℃,使病毒收获量提升 18%(某生物制药企业中试数据)。
三、全封闭负压循环系统,杜绝交叉污染风险
采用双重屏障密封技术:内层为磁力驱动泵(无轴封设计,泄漏率≤1×10⁻¹⁰mbar・L/s),外层为管路系统微负压运行(压力 - 50kPa±10kPa),防止外界空气倒灌污染。导热介质选用矿物油(粘度 35cSt,生物降解率<0.1%),经 0.1μm 精度过滤器(过滤效率 99.99%)实时净化,配合环路压力传感器(精度 ±0.01MPa)与液位监测系统(分辨率 1mL),实现介质无损耗循环。
在酶制剂发酵过程中,全封闭系统有效隔离杂菌侵入,使发酵液染菌率从传统开放式系统的 5% 降至 0.3% 以下(连续生产 300 批次统计数据);在 CAR-T 细胞培养场景,-5℃~40℃宽温域控制配合 CO₂浓度联动(控制精度 ±0.5%),使 T 细胞活率在 14 天培养周期内稳定维持 96%±1.2%,满足免疫细胞治疗的严苛要求。
四、多元生物工艺适配方案,赋能生物制造
1. 疫苗生产关键工艺控制
2. 重组蛋白表达工艺优化
3. 细胞治疗精准控温方案
为 iPSCs 诱导多能干细胞培养提供 37℃±0.05℃微环境,集成 O₂浓度动态调节(5%±0.5%),使干细胞克隆形成率提升 22%,且核型异常率控制在 1% 以下(染色体 G 显带分析结果),满足临床级细胞制剂生产要求。
五、智能化数据管理系统,满足生物制品追溯要求
配备符合 21 CFR Part 11 的电子记录系统,实时存储温度曲线(采样频率 1 次 / 秒)、灭菌日志、报警信息等数据(存储容量≥10 年),支持 USB 加密导出与 LIMS 系统无缝对接。7 寸彩色触摸屏界面经 GAMP5 验证,具备三级权限管理(操作员 / 工艺员 / 管理员),操作日志采用区块链技术存证,确保生物制品生产数据的完整性与可追溯性,全面满足 FDA、WHO 等国际监管机构的审计要求。
结语
该生物工程反应釜高低温一体机通过无菌工艺设计、精准温控技术与智能数据管理的深度融合,攻克了生物发酵过程中洁净度控制难、代谢热响应慢、批次一致性差等行业痛点。某生物制药上市公司应用数据显示,使用后疫苗批次合格率提升 20%,细胞培养污染率下降 80%,发酵周期缩短 15%,成为重组蛋白药物、病毒载体疫苗、细胞治疗等生物制品生产的核心装备,为生物制药产业实现从实验室研发到规模化生产的跨越提供了可靠的温度控制解决方案。

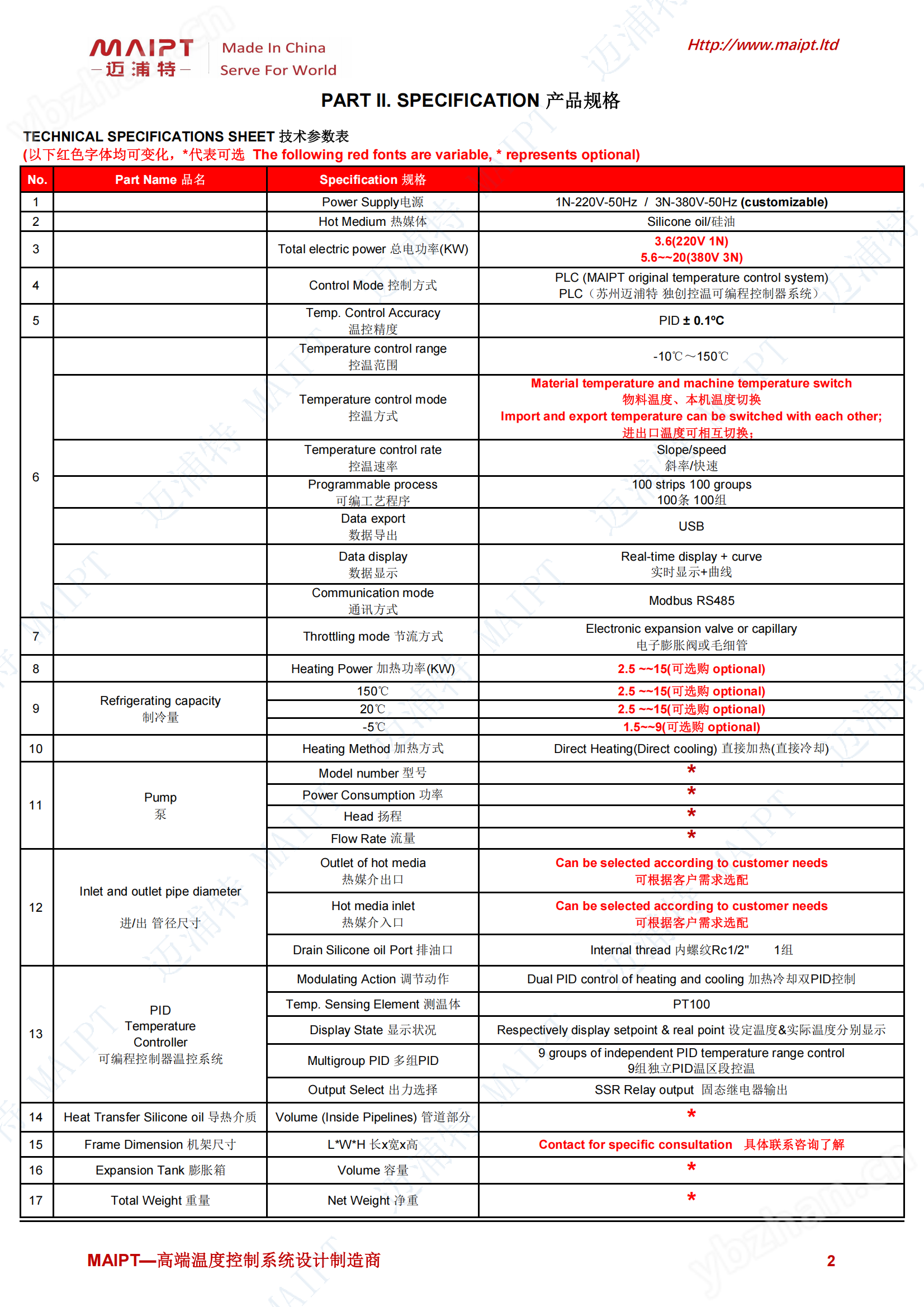
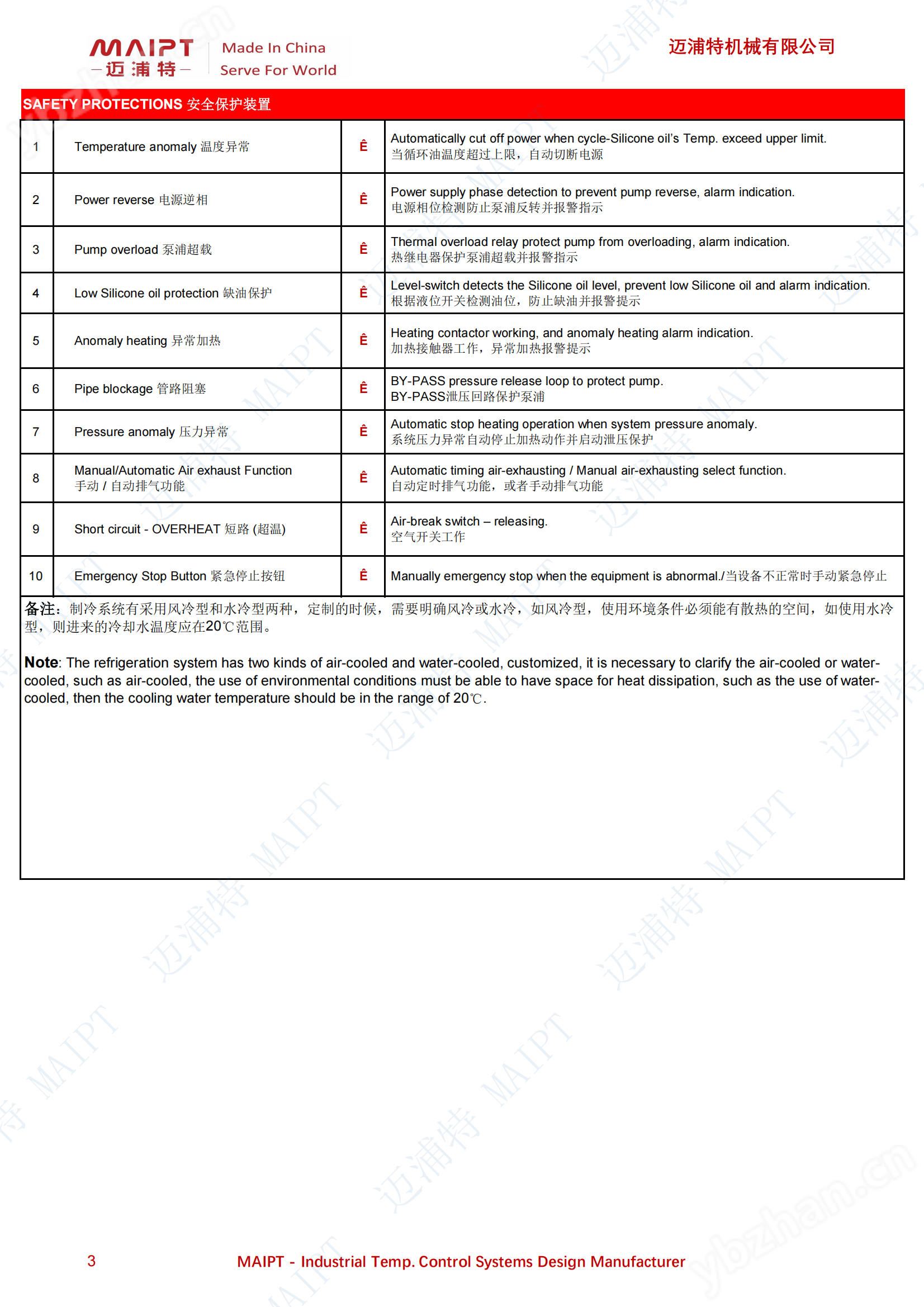
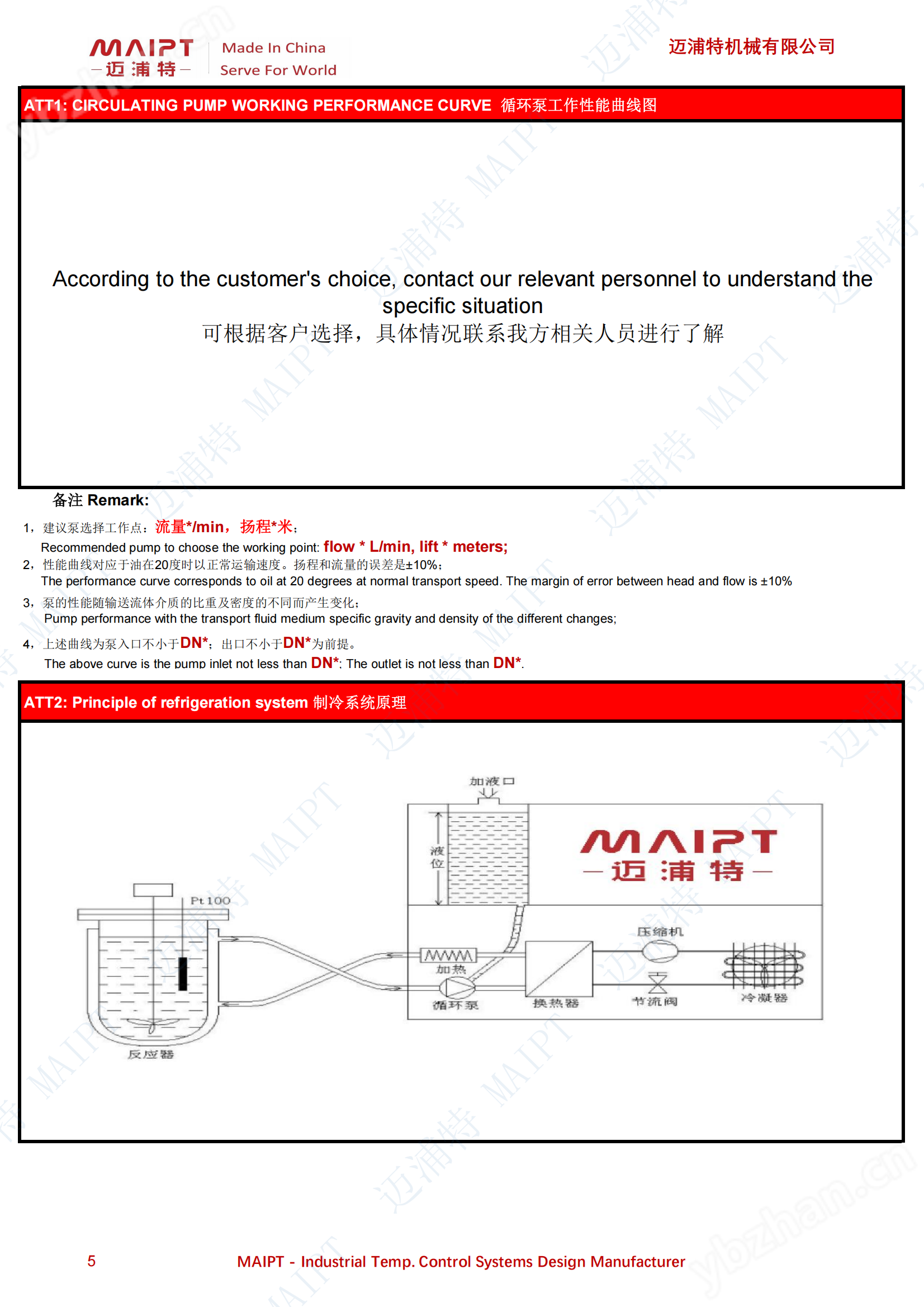
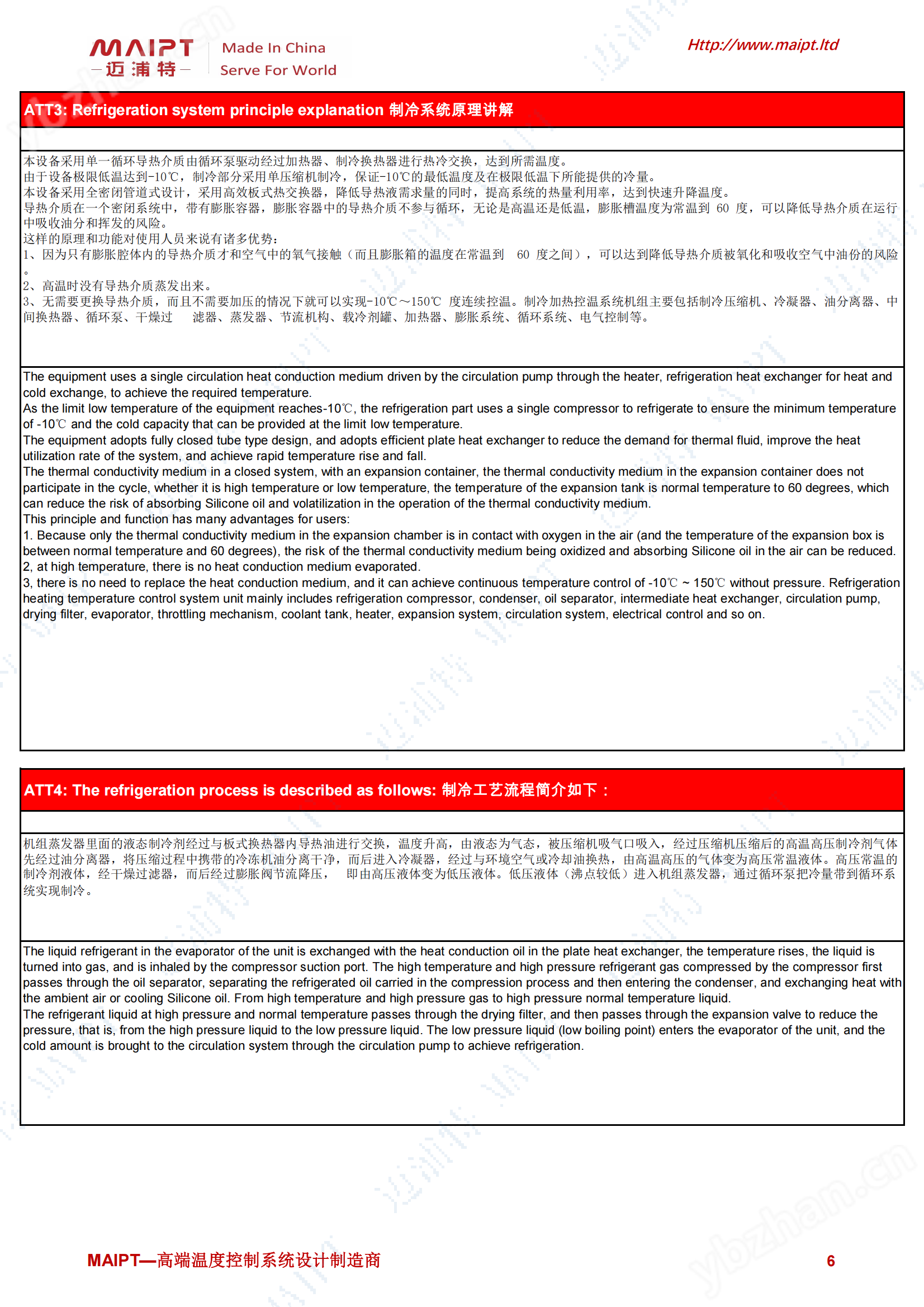
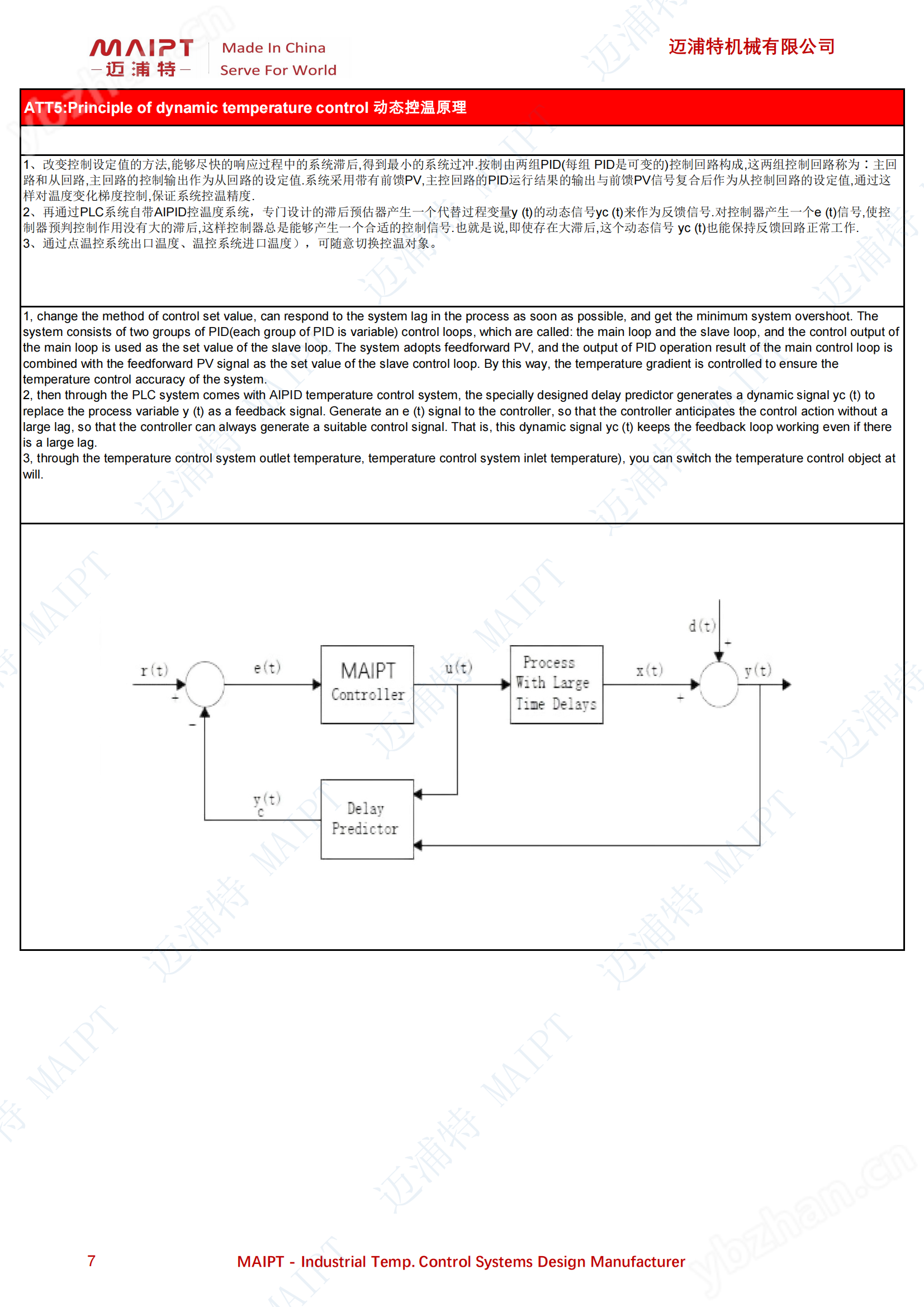
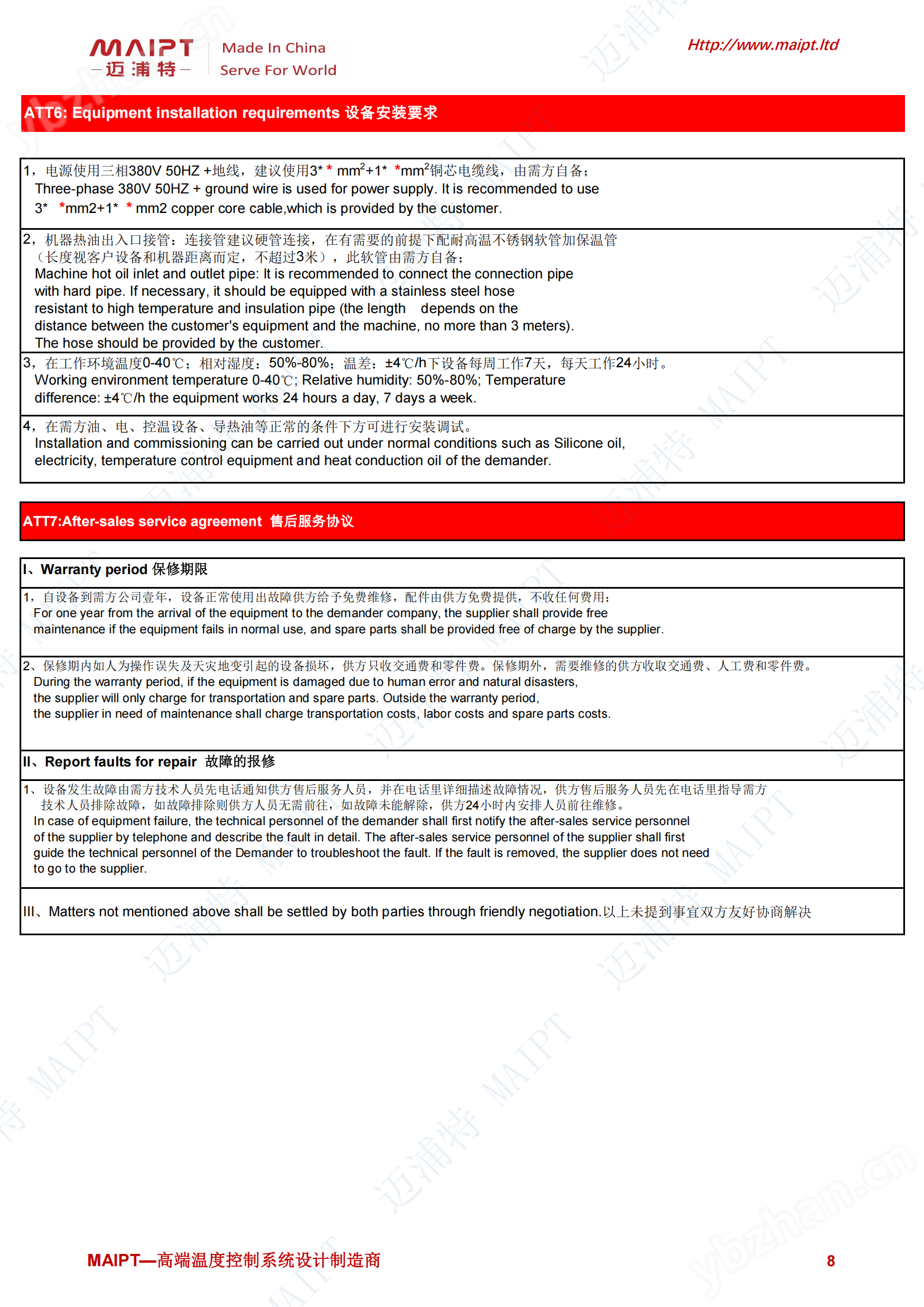
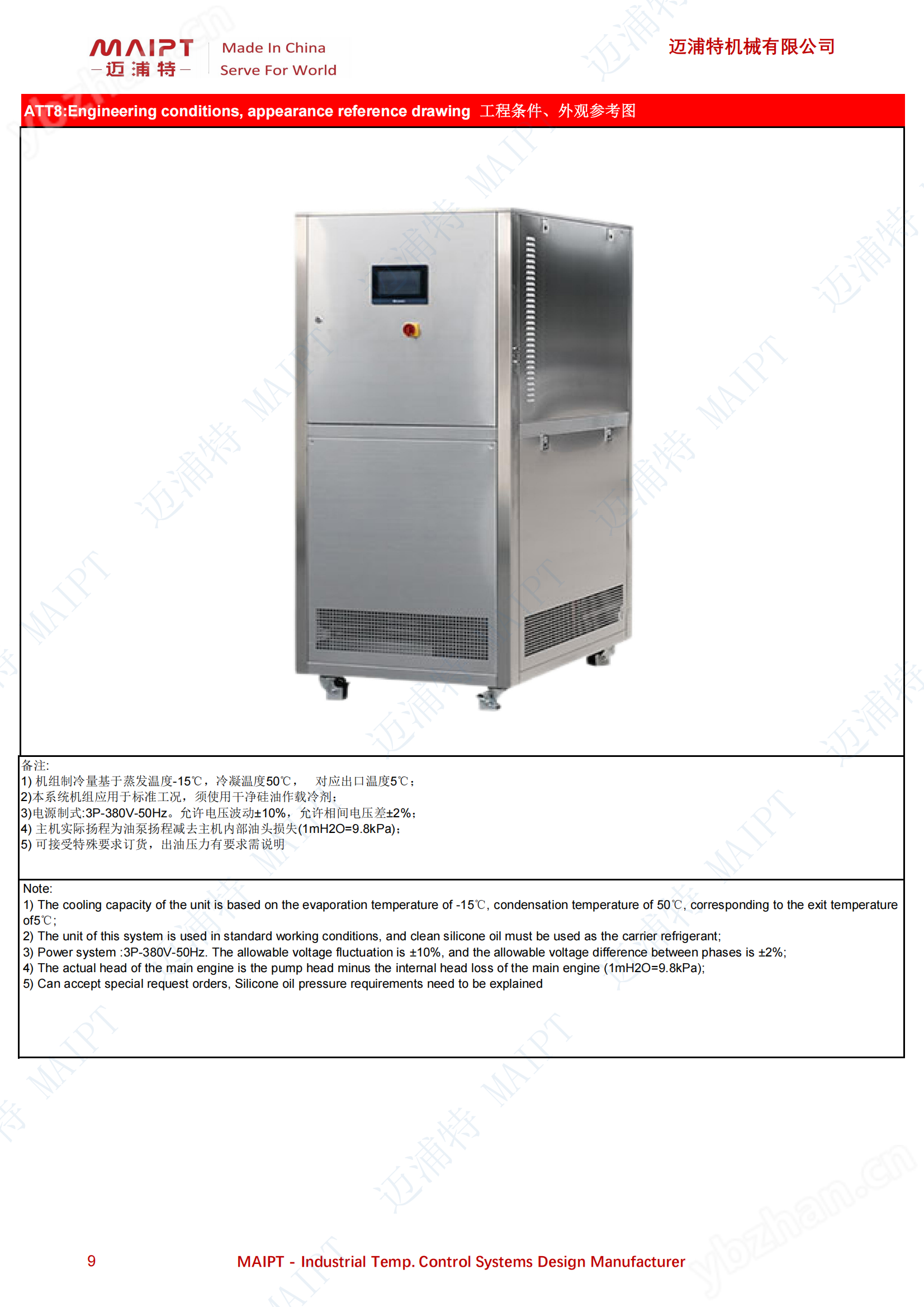

